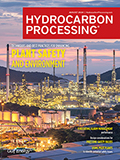
August 2024
Digital Features
On March 11, 2024, the U.S. Environmental Protection Agency published a final rule amending its Risk Management Program regulations. Here is what facility owners need to know about this new regulation.
Advanced budgeting for corrosion protection is critical to industrial facility management. Since the urgency of the matter is often not realized until a failure or accident occurs, the article provides several tips to help maintenance, purchasing or corporate teams start budgeting for preservation before an emergency happens.
To navigate this new world, organizations must find ways to bring in new technologies to support the limited personnel they have, but without increasing the complexity of those people’s jobs or overwhelming them with raw data they are not trained to use. The solution is to implement a predictive maintenance technology plan founded on a boundless automation vision of seamlessly moving contextualized data wherever it is needed.
Special Focus: Plant Safety and Environment
To demonstrate a new chemical process technology (flowsheet, raw materials, product) or improve an existing one, pilot plants are designed and operated at a scale between laboratory benchtop and commercial scale—often with specific goals for operability, product quality, economics and process safety. Identifying where potential safety, technical risks or uncertainties may occur is always a key goal in evaluating a new process.
The purpose of this article is to explain additional process considerations for pipework connected to PSVs, such as isolation valves, layout, orientation, forces and moments.
Industrial steam systems range from simple systems comprising a low-pressure single steam user to a complex system with multiple pressure levels, multiple generators and multiple users integrated with an onsite cogeneration facility. This article will present the typical CO2 emissions estimates for chemical and petrochemical facilities and describe options available to reduce these emissions through additional heat integration, fuel switching, and the use of heat pumps and electric boilers.
Process alarms are critical safeguards put into place on operating units to enable operators to avoid incidents that impact a company’s safety, reliability and bottom line. It is absolutely essential to any safe facility operation that alarms are properly managed and utilized to address real and consequential operational issues before they become incidents.
Petrochemical Technologies
In one recent project for a customer based in Asia, the authors’ company suggested the combination of distillation and crystallization techniques to obtain high-quality purified benzoic acid. Encouraged by the successful startup of this processing train, the customer began to schedule a second project. The authors’ company was asked to optimize the purification process to improve cost and operational efficiencies. The two existing columns, which remove lights and heavies, respectively, from the crude benzoic acid feedstock were investigated to identify key opportunities. The feasibility study based on the feed composition confirmed that the existing columns could be converted into a single dividing wall column (DWC).
Refining Technologies
Given the attractive demand projection, investors must understand the benefits and return on investment for natural and synthetic graphite routes. This article establishes the pros and cons for each, and specifically highlights the emerging opportunity for upgrading and repurposing smaller petcoke units to needle coke units, therefore contributing to fulfilling the rising demand for synthetic graphite.
Biofuels, Alternative/Renewable Fuels
Leading technology developers in the refining space are utilizing various catalysts to enhance the adjusted reaction chemistry, but this does not directly address how to optimize hydrogen utilization for the hydrodeoxygenation and isomerization/cracking processing steps. To ensure the right equipment outlay and calibration for these hydrogenation applications, replicating the process in a lab setting can help identify efficiencies and yield improvements for a fraction of the cost that a refiner would incur attempting to achieve that optimization through modifications at commercial scale.
Process Optimization
The catalytic alkylation process is very attractive to countries with high gasoline consumption and a sizable availability of LPG. This process can produce high-octane gasoline with low levels of contaminants, although there are high capital investment and operational costs associated with this technology.
Heat Transfer
Accurately estimating skin temperature and understanding the impact of refractory lining on thermal performance are crucial aspects of piping system design, operation and maintenance. By recognizing the multifaceted role of refractory lining in enhancing operational efficiency, mitigating risks and extending the lifespan of industrial piping systems, industries can optimize their processes and ensure the reliability and safety of their infrastructure.
Tanks, Terminals and Storage
Scientists from the authors’ company determined how best to combat persistent black mildew on aboveground storage tanks by first using a novel strategy to identify it. This discovery led to the identification of coating formulations with superior capacity to prevent mildew growth. The scientists proved the performance of the coatings by conducting field tests involving painting sample patches onto an ethanol storage tank.
Water Management
New personnel are often confronted with challenges that require knowledgeable and quick action, which they may have difficulty providing without thorough training. A very important—and sometimes overlooked—unit operation within these facilities is makeup water treatment for steam generators and other processes. Many cases have been documented in which makeup system upsets have led to boiler tube failures that partially or completely shut down unit processes. Parts 1 and 2 (September 2024) of this article serve as a guide for those employees who may be on a steep learning curve when it comes to makeup system understanding.
Among the available technologies of wastewater treatment to recover reusable water, zero-liquid discharge (ZLD) has become the most frequently used term in oil and gas refineries and petrochemical plants. It has been effectively used in the treatment of brine to maximize the recovery of freshwater or recycled water and to recover salt and other chemicals that are used in other industries.
This work is focused on the effect of cooling water parameters on admiralty brass tubes. The effect of high free chlorine on the corrosion rate of brass tubes has been investigated by scanning electron microscopes (SEMs) and eddy current test (ECT) methods and the laboratory results of the cooling water were determined and discussed. Also, the tendency of the feed water scaling indices that is LSI, PSI & RSI was calculated. The results show that a dezincification corrosion mechanism was observed due to the high-level free chlorine on the admiralty brass tube.
Trends and Resources
Emerson has released its Rosemount™ 9195 Wedge Flow Meter, a fully integrated solution consisting of a wedge primary sensor element, supporting components and a selectable Rosemount pressure transmitter.

- Transition Industries signs agreements for the Pacifico Mexinol Project, an ultra-low carbon chemical production facility 7/3
- Bangkok Airways introduces SAF on commercial flights 7/3
- EcoCeres secures SAF contract with British Airways to help reduce carbon emissions 7/3
- Air Liquide to invest up to $200 MM in Louisiana, U.S. to support industrial growth 7/3
- MOL completes the acquisition of LBC Tank Terminals 7/3
- BHP awards charter contracts for two ammonia dual-fueled vessels 7/3