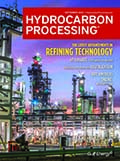
September 2020
Special Focus: Refining Technologies
Generating octane barrels has always been a tough road for refiners. In 2020, this road got a lot tougher with olefin saturation and octane destruction being collateral damage as refiners strive to achieve the sulfur limit in the gasoline pool.
With new legislative measurements implemented to combat global climate change, global environmental protection regulations are becoming more stringent. Tighter specifications are being enforced on gasoline pool components.
The negative impact of fossil fuels on the environment has become widely accepted, and our global society has begun to focus on alternative fuels. The pollution of the local, regional and global environment has become a primary concern.
Fluid catalytic cracking is one of the most important conversion processes used in refineries. This process converts heavy petroleum fractions into lighter, higher-value products, such as gasoline, propylene and others.
Process Optimization
Paraxylene production is a highly cyclical business that is subject to changes in the global economy and dependent on feedstock costs, alternative dispositions for aromatics, utilities costs and plant locations, among other factors. With the large PX capacity added by recently started crude-to-chemicals complexes and the expected impact of the economic recession on commodities demand, many aromatics complexes face a significant slowdown in the coming months or, possibly, years.
Catalyts
Refiners are continually challenged to maximize economic gain in the face of cost pressures and plant operating constraints. The fluidized catalytic cracking unit (FCCU) plays an integral role in the optimization of the facility. FCC catalyst is often one of the largest budget items in the refinery. Therefore, the balance between FCCU performance and catalyst costs has a significant impact on refinery profitability.
In a growing and competitive industry, ethylene producers are turning to catalyst suppliers for solutions to innovate. Until recently, a solution to the difficulties inherent to acetylene hydrogenation in ethylene plants has challenged the catalyst industry. Due to their lower total production cost, “front-end” process flowsheets are now predominantly selected for new projects.
HP Awards Finalists 2020
This special section details all finalists within each category for the fourth annual <ital>HP</ital> Awards. The winners will be announced on Oct. 1.
Heat Transfer
As part of the U.S. Environmental Protection Agency’s (EPA’s) maximum achievable control technology (MACT) fired heater inspection program, the authors’ company has inspected nearly 1,000 heaters since the program started in 2015. These inspections have revealed all types of flames—the good, bad and ugly. Here, good is defined as no changes are needed; bad is defined as changes are needed where the conditions are not likely dangerous; and ugly is defined as immediate changes are needed because the conditions are potentially dangerous.
Valves, Pumps and Turbomachinery
Tank and terminal facility profitability ultimately rests on a handful of key performance indicators (KPIs). The ability to maximize tank capacity utilization—while minimizing the time it takes to load and unload ships, trucks and rail cars—drives the bottom line. All those transfers must happen quickly and accurately, while avoiding product contamination.
Digitalization
Operational technology/information technology integration is required for sharing information among all levels of manufacturing organizations to achieve profit-driven operation, which helps process industry companies implement real-time production performance improvements that are aligned from the management level to the plant floor.
Industry 4.0 technologies apply to new opportunities for training and upskilling to improvements in production and risk reduction. Businesses want to achieve operational excellence, and digitalization is the key to helping organizations move forward on their digital journeys.
Refineries and petrochemical plants face similar challenges in daily operations. Each must mitigate risk, anticipate maintenance, optimize operations and minimize expenses. To achieve these goals, plant personnel rely heavily on data to drive decisions.
Columns
Over the next two months, <ital>Hydrocarbon Processing</ital> will host two separate events for a global audience. One will gather the brightest minds in the industry to share the latest innovations and technologies in the industry, while the other will recognize the leaders in advancing the industry toward safer and more reliable, sustainable and profitable operations. Both events—<ital>Hydrocarbon Processing’s</ital> IRPC and the HP Awards—will be streamed on digital platforms and free to view.
Like many thousands of educational and operator training-related endeavors, reliability improvement training was abruptly suspended when the COVID-19 pandemic interrupted daily life as it was known prior to 2020.
The implementation of a project schedule must avoid slippage, which can lead to budget overruns and delays in commissioning and production. Conversely, a reduction in project schedule results in an early startup of the plant, creating advantage for stakeholders. Customers often demand reductions in schedule timelines, which can be difficult for engineering, procurement and construction (EPC) contractors to implement. New innovations like concurrent engineering, modular construction, prefabricated pipe racks and structures, etc., are already in practice.
Piping represents a significant part of the plant cost, ranging from 15%–25%.1 Materials stored in warehouses or storage facilities cost companies in terms of personnel, materials, time, space, insurance, risk, etc. This article proposes cost-saving strategies for inventory reduction. Further, it emphasizes consistent naming conventions to avoid creating duplicate/redundant items.
There is much discussion and information about digital transformation, but many HPI companies are taking a different approach to integrating new digital technologies and to differentiate themselves from their peers, and are seeing truly transformative business results. HPI digital technology leaders reveal the following five best practices.
Trends and Resources
Over the past several years, <ital>Hydrocarbon Processing</ital> has honored the feats of capital project excellence with its Top Projects Awards. The winners and nominees encapsulate important contributions to the global hydrocarbon processing industry, whether that is through significant capital intensity, diversifying product offerings or adding a significant amount of refining and/or petrochemical processing capacity.
Progress in the driverless car segment has served to illuminate one of the major future goals in industrial and process manufacturing: autonomous operations in process plants—in other words, the autonomous plant. While AO for process plants has received interest from the process automation and control industry, limited serious discussion has taken place in the process operations and IT domains.
Each year, <ital>Hydrocarbon Processing</ital> hosts two technical conferences focusing on the latest in technologies that are optimizing plant operations and production. <ital>Hydrocarbon Processing’s</ital> IRPC brings together leaders in the refining and petrochemical industries to discuss best practices and advancements in the HPI.
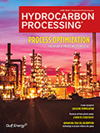
- Petrobras wrapping up due diligence to buy back refinery from Mubadala 7/26
- US court rejects EPA denials of 2022 small refinery biofuel waivers 7/26
- Mexico seeks more 2025 fuel import deals after refinery delays 7/26
- PETRONAS, Eni and Euglena reach FID to construct a biorefinery in Malaysia 7/26
- ExxonMobil signs carbon capture agreement with CF Industries in Mississippi (U.S,) 7/26
- WoodMac: LNG truck sales impacting Chinese road diesel demand 7/26
- Digital Exclusive: SPECIAL FOCUS: Digital Technologies—Utilize process simulation digital twin to optimize condensate yield
- Digital Exclusive-Flare system design: Liquid pockets in flare headers
- Hydrogen-rich content gasoline: A new concept for paraffinic gasoline reformulation
- Alarm rationalization at Kuwait National Petroleum Company (KNPC) refineries