Webcasts

Sponsor: Schneider Electric
Introducing an entirely new concept for improving petroleum and petrochemical supply chain performance with the advent of Unified Supply Chain Management for assay management, feedstock evaluation, feedstock trading, plant and network planning and scheduling could be quite disruptive.
This webinar will discuss the unified concept of this new solution and its impact on the human experience, with special emphasis on increased worker productivity as a result of improved data management, interactivity with the software, and the ability to develop entirely new and more effective work processes.
View On Demand
Sponsor: Sherwin-Williams
Hydrocarbon processing plants are challenged with protecting assets against both corrosion and fire damage. Corrosion poses a great threat to structural integrity – especially in a fire scenario. Corrosion underneath fireproofing can be hard to detect, and when it’s found, the costs to mitigate the corrosion and replace fireproofing materials can overwhelm plant maintenance budgets. This presentation highlights differences in fireproofing types and how each type correlates with corrosion potential. It will help owners and specifiers select the proper fireproofing materials to last the desired life of their assets, while eliminating the threat of corrosion.
View On Demand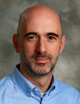
Sponsor: Honeywell UOP
With reduced crude oil prices, the Oil & Gas industry faces a rapidly changing market place combined with lightening-speed advances in technology. The question facing refining and petrochemical producers is how to successfully adapt to the challenges by investing in technology that leverages insights from big data and drives business growth with operational improvements, increased reliability and higher margins.
Join Honeywell UOP’s Connected Performance Services's Business Leader, Christophe Romatier, and Sr. Product Line Manager, Katherine Jones, for an informative webinar. They will highlight a scenario around a new cloud-based service from Honeywell Connected Plant that targets these challenges, provides industrial users with around the clock monitoring of plant data and rigorous simulations, and offers on-going operational health checks and recommendations to close performance gaps and drive operational excellence.
View On Demand
Sponsor: AspenTech
Join us for a live webinar featuring Braskem, the largest petrochemical company in Latin America. In this webinar attendees will learn how Adaptive Process Control in Aspen DMC3 was implemented to lower energy usage by 20%, increase production rates and reduce process variability. The project was completed using existing internal resources, yielding outstanding results and great operator acceptance. Livia Tizzo, Process Control and Automation Engineer, will detail how Braskem implemented several APC projects on ethylene units across the organization.
View On Demand
Sponsor: Schneider Electric
The prolonged supply-demand imbalance in the oil markets is causing crude prices to stay low for a longer period of time, benefiting downstream operations due to lower feedstock costs and spurring demand for petrochemicals. Today, companies are expanding their ethylene cracker operations to capitalize on the strong demand, and utilizing advanced analytics and design simulation tools to do “more with less” in the current volatile environment.
In this webinar, learn how you can use simulated design tools and advanced analytics to:
- Reduce CAPEX through optimized process design during the FEED stage
- Reduce OPEX through optimized process conditions during operations
- Improve asset ROI through early warning of asset failure before it happens, reducing unplanned downtime and improving asset availability.

Sponsor: Johns Manville IIG/ITW Insulation Systems
CUI is a major concern with many resources dedicated to corrosion prevention, but there isn’t a one-size-fits-all solution. An effective CUI prevention strategy must consider the elements of an entire insulation system. Join Johns Manville Industrial Insulation Group and ITW Insulation Systems for a live webinar, Combat CUI: How to Combine Insulation & Jacketing to Inhibit CUI. Receive PDH credits for attending the live webinar.
View On Demand
Sponsor: PTC
Whether your operation is upstream, midstream, or downstream – your organization needs a solution that connects disparate assets, systems, databases, and data/naming conventions. The industrial IoT enables organizations to build smart system architectures that avoid these classic data silos to prove concepts and produce business value.
Industrial IoT applications can improve efficiency in Oil and Gas operations:
- Operations data management: what data can be relieved to lower the risk of overburdening the operational host, i.e., SCADA or DCS?
- Product life cycle management as a service or a product: how can we use machine learning to more effectively monitor pump asset anomalies and manage the care for better production results?
By the end of 2017, we predict there will be large quantities of proof of concept (PoC) industrial IoT applications in Oil and Gas. There is so much potential. To effectively bring the power of IoT to your organization, a smart approach is to choose a project that can be implemented quickly and has a clear, measurable business value. Start simple, succeed, and apply your learning to the next project.
View On Demand
Sponsor: Schneider Electric
Refineries and petrochemical plants are challenged with sustaining and improving margins, and retaining operational knowledge from a retiring workforce. The next focus of operations improvement requires embarking on a journey of digital transformation, through elimination of wasted work, automation of work flows and “transformation” — changing when, where, which and how work is performed and evolved. Over time, digital operations management becomes self-evolution to achieve improved profitability. Learn in this webinar how you can achieve the next level of operational efficiency for your plant.
View On Demand
- RIC Energy and Siemens to jointly develop renewable H2, green ammonia and eFuels 6/2
- Trump administration (U.S.) axes $3.7-B in green energy projects 6/2
- Petroecuador declares emergency at Ecuador's biggest refinery after fire damages 5/30
- U.S. administration considers plan to clear record backlog of small refinery biofuel waivers 5/30
- Sinopec sets up $690-MM hydrogen-energy-focused venture capital fund 5/30
- Wartsila bets flexibility key for ethanol power generation in Brazil 5/30