Webcasts

Sponsor: Schneider Electric
While refinery scheduling paves the way for a refiner to generate the inherent value within an economically-optimized refinery plan, the real value is realized in the physical processing of refinery feedstocks and generation of marketable products. Refiners often face the challenge of ensuring synchronization between what has been defined as scheduled operational sequence and what is actually being executed in the operations environment. This synchronization challenge means the schedule is continuously impacted by internal and external changes and, as such, is undergoing continuous change. In this webinar, several strategies to ensure synchronization between scheduling and operations will be discussed (especially, in oil movement operations where the majority of scheduling instructions exist).
View On Demand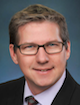
Sponsor: AspenTech
Using the latest prescriptive analytics and predictive modeling solutions, organizations extend the life of aging equipment, increase uptime, and achieve optimal process performance that surges profitability. Register today to hear from ARC Advisory Group’s Contributing Analyst, Peter Reynolds, as he shares his insights on:
- Why predictive and prescriptive analytics offer such promise, and how to select the target project within your company.
- The breakthrough approach combining data analytics with model-based process knowledge.
- Roles of big data analytics, machine learning prescriptive approaches, model-based analytics and the Industrial Internet of Things (IIoT).
Additionally, Ron Beck will talk about case studies involving AspenTech’s Asset Performance Management (APM) suite.
View On Demand

Sponsor: Johns Manville Industrial Insulation Group
As the need for real-world, field-validated CUI testing becomes more and more relevant in the industrial insulation industry, we find ourselves on the cusp of a new generation of corrosion test methods that could influence your corrosion strategy.
Join Leo Caseres, Ph.D., from Southwest Research Institute, and Ames Kulprathipanja, Ph.D., from Johns Manville, for their live webinar, CUI Research: The Critical Components & Findings. The co-presenters will outline a new, accelerated CUI test with field-validated results, as well as discuss what the industry can expect to see for the next evolution in corrosion testing.
The webinar will be held on Wednesday, June 7, 2017, at 2 p.m. EDT / 6 p.m. UTC, and will be followed with a live Q&A in which any participant may submit questions to our presenters. Johns Manville Industrial Insulation will provide a Certificate of Completion for attending the live webinar which can be submitted for credit toward Professional Development Hours (PDH)*.
The experts in the industry will discuss the following topics:
- The cost and impact of CUI
- Critical components to successful, objective research
- The lack of end-user field testing and the impact on the industry
- Example and test results from cutting-edge, real-world CUI testing
- Opportunities to get involved in future testing and research.

Sponsor: Schneider Electric
The petrochemicals boom has officially begun as the natural gas prices fell due to new technological advances. By Q2 2018, an additional 15.6B lb/yr ethylene production are planned – translating to $16.5B investment in the form of new plants or upgrading the existing plants to utilize natural gas and to produce more ethylene. This webinar will provide how steady state and dynamic simulation services can be used to identify plant bottlenecks, retrofit existing plants and design new plants for safer, smooth and optimum operations. Best practice modeling will include steam systems, compressor control systems, relief and flare studies, highly integrated ethylene plants, and ethylene plant optimization.
View On Demand
Hydrocarbon Processing's well-known Heinz Bloch webcast series is back by popular demand. The first webcast offered under Mr. Bloch's latest series, "Unusual Fluid Machinery Failures," outlines the most effective and readily implementable failure analysis strategies. During the 60-minute presentation, Mr. Bloch will analyze proven and effective approaches that have been readily implemented by successful organizations. Two interesting field examples will be highlighted; both approaches were adopted by a number of job functions in the HPI.
Mr. Bloch is Hydrocarbon Processing’s Reliability/Equipment Editor, and one of the HPI’s foremost experts on improving machinery reliability.
View On Demand
Sponsor: Schneider Electric
Every day the refining and petrochemicals industries are faced with new demands—demands for higher margins, higher output, enhanced worker productivity, increased efficiencies and higher productivity. But the reality is that most plants have old equipment not designed for today’s feedstock, and operators that are either ready to retire, or inexperienced and ill-equipped to run the refinery at peak performance.
Refiners require a set of tools that empower them to make decisions given a wide range of operating conditions, including the availability of alternative feedstock, process disturbances that require immediate action, shifts in product margins or changing product/utility prices that require operating changes for optimal profitability. This webinar will show how advanced tools can deliver a:
- 2–5% improvement in energy reduction, yield improvement, etc.
- $0.05 to $0.25/bbl improvement in process profitability
- Payback period of six months or less.

Sponsor: Schneider Electric
The step change in technology can be leveraged to enhance your workforce to increase safety, productivity, teamwork and efficiency. Any company that implements any of the available technologies, we see an immediate impact on profitability. Regardless of the current workforce enablement solutions that you employ, there are technologies that can be rolled out on your infrastructure including mobile technology, business process management, operator training, virtual reality or augmented reality.
View On Demand
The dynamics of the hydrocarbon processing industry (HPI) are constantly changing. New downstream capacity additions, emerging supply/demand regions and technological advances are changing product trade flows and the way the industry invests in capital-intensive projects. With over $1.6 T in announced projects globally, it is imperative that HPI companies receive the most up-to-date and valid information on market trends, and the future development of the downstream processing industry.
The editors of Hydrocarbon Processing have been providing their global insights on investments and trends in the refining, petrochemical and natural gas/LNG industries for over 40 years. Hydrocarbon Processing’s downstream forecast is a one-of-kind resource providing HPI professionals with the data and tools to make informed decisions, plan strategically and recognize new opportunities in the global HPI.
During this live webcast, Lee Nichols will provide comprehensive detail for capital, maintenance and operating expenditures, as well as major economic, environmental and political market trends by region and sector; and how these forces will influence the industry in the near-term.
View On Demand
- Petroecuador declares emergency at Ecuador's biggest refinery after fire damages 5/30
- U.S. administration considers plan to clear record backlog of small refinery biofuel waivers 5/30
- Sinopec sets up $690-MM hydrogen-energy-focused venture capital fund 5/30
- Wartsila bets flexibility key for ethanol power generation in Brazil 5/30
- Lotte Chemical Titan signs contract to buy naphtha from Aramco Trading Singapore 5/30
- India's May diesel exports to Southeast Asia seen at multi-year highs on higher margins 5/30