Webcasts
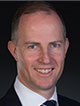
Sponsor: AVEVA
As the world emerges changed by the covid-19 shutdowns, the rate of digital transformation necessitated during the pandemic will carry us into the future of sustainable, digital and connected plants. New and existing industrial plants will depend on an influx of innovation, flexibility and collaboration driven by technologies like the cloud, data-centric engineering and 3D visualization to prepare for what's ahead. Join Julien De Beer, AVEVA’s Head of Product Strategy for this 1-hour session to hear how AVEVA’s EPC 4.0 approach can help you achieve your future plant strategies, including:
- A proven framework to drive greater engineering & execution quality and efficiency
- How to create a culture of data-centric, integrated, collaborative working
- Requirements for building and maintaining Digital Twins on greenfield and brownfield projects
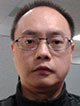
Sponsor: Honeywell
Non-aqueous corrosion issues continue to be a major concern for refining as market growth leads to feedstock with increasing impurity content, leading to higher potential for corrosion damage. Naphthenic acid and sulfidic corrosion (termed crude corrosivity) in crude refining are key corrosion mechanisms contributing to asset degradation and failure in different areas of atmospheric and vacuum distillation units, such as in transfer lines and side cut piping. Accurate quantification of corrosion due to these factors is critical to safe crude unit operations and gives refiners the ability to work with opportunity crudes at a higher level of confidence and safety. In this webinar we will present a comprehensive approach to predict crude corrosivity in naphthenic acid- and sulfidic-dominated systems as a function of critical environmental parameters such as: Total Acid Number (TAN / NAT), Sulfur (H2S) content, temperature, hydrocarbon content, flow regimes and wall shear stress.
View On Demand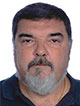
Sponsor: Aggreko
Aggreko Process Services is a unique dedicated Process Engineering team within Aggreko that work alongside unit operations to deliver fast-track high value solutions that enhance Refinery and Petrochemical Plant capacity and efficiency. This session will explore multiple Dense Air applications and their benefits in a refining or chemical facility and take a closer look at:
- Main Air blower constraints in the FCC
- Refrigeration of reactor/ regenerator at the FFC during shut down
- How dense air can improve Turbogas power output
- An all-round view on possible applications of dense air to optimize Petrochemical Plant Processes
At Aggreko we understand the huge pressure process industries face to continually improve yield, upgrade capacity, and respond to ever-changing market conditions. Our advanced process knowledge and proven experience delivers innovative solutions that are operationally safe and reliable. Join our webinar to learn how our process engineers can help you achieve ultimate process optimization.
View On Demand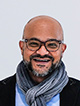
Sponsor: AVEVA
From changing regulations to an evolving new normal, capital projects face rapidly shifting market dynamics. In this ever-evolving landscape, how do you prepare for what’s ahead? Short answer – Foster flexibility, transparency and collaboration.
Join Amit Kar, from AVEVA, for a 1-hour session where he will discuss how EPCs and owner operators can leverage technology to build resilience now while also laying the foundation for the plant of the future. During the session, he will provide expertise on how the right mix of people, technology, and processes can create structure without hindering creativity at your company to help you achieve the following:
- Create automated transparency in capital project engineering and execution
- Leverage every interaction to build trust between the Owner-Operator and the EPC
- Accelerate the path to operational nameplate capacity
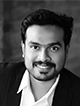
Sponsor: GE
As investment in analytics continues to increase year after year, one function that has remained relatively status que from leveraging new techniques is the mechanical integrity function. While 87% of oil and gas companies have invested in analytics – 68% of companies are still using homegrown software or no solution at all for asset integrity management. While the objectives of avoiding loss of containment, demonstrating compliance, and ensuring high availability units hasn’t changed new dynamics could be putting your program at risk.
In this session we will discuss:
- Emerging trends and factors that could be putting mechanical integrity programs at risk
- A programmatic and technology framework to streamline KPI’s and work processes
- How analytics can be embedded in Mechanical Integrity software and work processes to advance the objectives of compliance, containment, and high availability plants
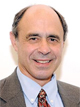
Sponsor: AspenTech
Hydrogen and carbon capture have become focal points as energy and chemical companies look to reduce emissions and achieve net-zero carbon targets. But what’s the best approach?
Please join Hydrocarbon Processing Executive Editor Adrienne Blume and AspenTech Industry Expert Ron Beck as they discuss how new digital tools integrated with existing technology give you a competitive edge to reduce your carbon footprint while greatly advancing your overall sustainability efforts. Learn how new innovations enable you to:
- Combine process, AI and risk modeling to drive optioneering, innovation and economics
- Scale rapidly from demonstration plants to multiple industrial facilities
- Integrate systems risk and energy modeling into existing assets
- Apply advanced analytics and modeling to ensure operability of new technologies
In addition, customer case studies will be shared to demonstrate how modeling has been applied in support of carbon capture, green and blue hydrogen, and fuel cells.
There will be a Q&A session following the event. We encourage you to join the conversation by submitting questions when registering.
View On Demand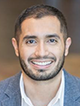
Sponsor: Honeywell
Maintenance tasks in process industries are becoming ever more complex. New generations of frontline professionals are now tasked to maintain a wider range of intricate production assets. They now need to climb the learning curve faster to bring assets back to the optimal operational states that support the organization's production goals. Join this webinar to discover the mobility technologies that are enabling new generations of frontline maintainers to solve problems faster. We will explore through practical demonstrations how to enhance team collaboration and provide access to information for field teams to be more effective and reduce the time on task.
View On Demand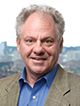
Sponsor: LNS Research
Autonomous plant and remote operations are two areas that have generated strong interest due to COVID-19. LNS Research, the experts in Industrial Transformation, recently conducted a survey of 300+ respondents across several industries to examine Autonomy within plants and throughout the entire value chain.
Join Hydrocarbon Processing and LNS Research on Tuesday, March 30th, 2021, at 11 a.m. EDT for an informative webcast on Autonomous Operations. Analyst Joe Perino will discuss LNS’ latest study on Remote Operations and Autonomy and how they link to Industrial Transformation success.
In this webcast, discover:
- Characteristics of Autonomous systems and why you should choose Autonomy
- Challenges of Remote Operations and how you can successfully navigate them
- How leadership and organizational culture directly impact Autonomous Operations
- Next-Gen technology adoption and where companies are investing
- What Industrial Transformation Leaders do differently than Followers to accelerate Autonomy
- Recommendations on how you can effectively implement Autonomy

- Update: IATA airlines chief warns aviation industry falling behind on net-zero 4/7
- Improved recycling of plastic from packaging waste 4/7
- India not to raise petrol, diesel retail prices despite tax hike 4/7
- China teapot oil refiners improve run rates but demand woes, sanctions weigh 4/7
- U.S. refiners' shares hit near 2-yr lows as Trump tariffs spur fuel demand fears 4/7
- Update: India's fuel demand hits 10-month high in March 4/7