Webcasts
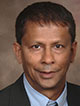
Sponsor: Chevron Lummus Global, LLC
As the world transitions toward a lower-carbon energy supply, the industry will need an enormous investment for future greener energy supply. Energy producers, petrochemical manufacturers, and technology providers are developing creative and cost-effective solutions to transform today’s refineries into tomorrow’s energy hubs. Join this webcast to learn how Chevron Lummus Global (CLG), a market leader in resid hydrocracking, employs its LC-FINING technology and Eni’s Slurry Technology (EST) to introduce sustainability to conventional resid upgrading. Subject matter experts will share insights on producing chemical feedstocks, co-processing circular and renewable feedstocks and how to tackle challenging bio-renewable resid or circular feedstocks.
View On Demand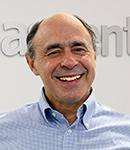
Sponsor: AspenTech
Carbon Capture and Storage (CCS) will be an essential pathway as industries move to net zero. The ability to handle CO2 at both emission sources and directly from air, together with long-term storage in the subsurface, make CCS a crucial part of the energy transition.
Join AspenTech experts to learn how innovations in digital technology support end-to-end CCS, with faster, widespread scale-up and improvements in economics and efficiency. Learn how you and your teams can:
- Use rigorous modeling and economic analysis for rapid design and scale-up of carbon capture processes
- Evaluate all current and new technology areas (such as liquid and physical solvent absorption, zeolites, membranes and other approaches) to find the most viable solution for your use cases
- Leverage subsurface models to select depleted reservoirs and aquifers for CO2 storage that meet technical and economic criteria
- Support optimized control and ongoing operator training to reduce risks and ensure proper CO2 storage
You’ll see how chemical simulation models evaluate CCS approaches, such as converting CO2 to carbonates. Now is the time to adopt an end-to-end carbon capture and storage solution tailored to your needs.
We encourage you to join the conversation by submitting questions when registering for the event.
View On Demand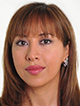
Sponsor: AspenTech
With the rapid escalation of energy prices and geopolitical risk in Europe, energy security has moved to center stage. At the same time, energy and chemical companies need to innovate and transform their business strategies to meet sustainability and profitability goals. Digital solutions are emerging as a strategic tool to help organizations navigate volatility short and long term.
Please join Hydrocarbon Processing Technical Editor Sumedha Sharma for a lively discussion with industry experts Dr. Carole Nakhle, Crystol Energy CEO, and Ron Beck, Senior Industry Marketing Director from AspenTech, as they provide insights on the following topics and more:
- Economic and resource challenges associated with meeting energy transition goals
- Barriers to electrification, energy security, energy efficiency and carbon removal
- Role of technology in meeting global resource demands while advancing sustainability
- Impact of global conflict on energy policy priorities
Sign up today to gain valuable insights to help you evolve your energy transition strategy. There will be a Q&A session following the event. We encourage you to join the conversation by submitting questions when registering.
View On Demand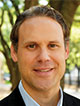
Over the past several years, the hydrocarbon processing industry (HPI) has been engaged in a whirlwind of peaks and valleys. This included robust capital expenditures to build new refining, petrochemicals and gas processing/LNG capacity to satisfy future demand. However, COVID-19 created a fundamental shift in the capital projects market, leading to delays and even project cancellations. As lockdowns ease, dormant projects are receiving new life. What nations are investing in these projects? Why are they investing in new capacity? What major trends are driving the HPI globally?
During this live webcast, Lee Nichols will provide a mid-year update on capital projects around the world, as well as major economic, environmental and political market trends that are shaping and influencing the industry in the near-term.
View On Demand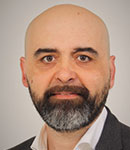
Sponsor: Lummus Technology
Shell and tube heat exchangers equipped with high-pressure breech-lock (or screw-plug) closures are used extensively in the hydroprocessing industry for high pressure and temperature services when there is a requirement to open the exchanger for inspection and maintenance and when a leak-free operation is paramount. The breech-lock closure allows for sealing adjustments without being dismantled, providing quicker opening and closing operations compared to TEMA closures.
Join us for a virtual introduction as Lummus Technology presents the latest innovation in breech-lock closures. This webcast will highlight the limitations of today’s breech-lock technology, explain Lummus’ path in development, and showcase how the next generation raises the bar to deliver a closure that is more easily operated and maintained.
View On Demand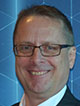
Sponsor: Siemens
Workforces around the world make vital operational decisions everyday. However, the plant related information required to stay in control and make the right decision at the right time is not always available or accessible. Business as usual for many companies means struggling with silos of data and lost opportunity across every shift.
To continuously improve, you need to continuously measure and identify deviations from plan, then make informed decisions in a timely manner. This is only possible if the workforce has easy access to the data they need to see, in the way they need to see it.
Siemens and IT Vizion help companies around the world equipping their workforce with real-time decision support, increasing profits and reducing time-to-value.
Join our webinar to learn how companies have enabled proactive decision making with complete, real-time, situational awareness using XHQ software.
View On Demand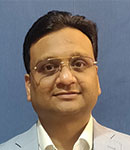
Sponsor: Topsoe
With the ever-increasing commitments to CO2 reduction, the path has been set and it is now time to deliver on that promise.
Today, Topsoe technology is producing one third of the world’s hydrogen; And as the technology leader, Topsoe’s mission is to deliver blue hydrogen at the necessary mega scale to reach our net zero targets.
Join us for a discussion on the growing global demand for hydrogen and on its new applications in the clean energy sector. Learn about the processes to produce blue hydrogen, with ultra-low carbon intensity at the lowest levelized cost, at mega scale. Find out how industry leaders are planning on decarbonizing their existing assets by using blue hydrogen and gain valuable insight into the respective international incentives for producing low carbon intensity hydrogen.
View On Demand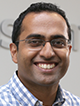
Sponsor: AspenTech
Refineries are always looking to reduce their energy use and carbon footprint. Here is a unique opportunity to learn how a major refinery in Asia drastically reduced steam consumption by deploying a real-time digital twin that was built using Aspen HYSYS® and works with their Aspen DMC3™ advanced process control (APC) system.
Join refinery experts as they discuss their experiences with the solution, which was recently awarded the “Best Digital Twin of 2021” from Hydrocarbon Processing. Learn how you can:
- Save energy with better process optimization using insights from online digital twins
- Gain real-time insights to key operational parameters that are not directly measurable
- Adopt best practices on maintaining and building an online digital twin
Discover how you can implement digital twin solutions to help your refinery meet sustainability and profitability targets.

- Sumitomo Chemical achieves scale-up of its process for producing propylene directly from ethanol 8/20
- EcoCortec, Jakob Schober GmbH awarded sustainability award for closed-loop circular films solution 8/20
- Sanctions-hit Indian refiner Nayara turns to ‘dark fleet’ 8/20
- EIA: Crude and gasoline inventories fall, distillates rise 8/20
- Czech refinery outage forces Orlen Unipetrol to seek state help to meet diesel demand 8/20
- China’s Sinopec Shanghai Petrochemical first half profit slides 8/20