Webcasts
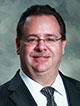
Sponsored by: Honeywell UOP
Annual capacity additions of 6 MM MTA ethylene and 4 MM MTA propylene are needed to meet the continued demand growth of light olefins. Concurrently, demand for transportation fuels is declining in some regions and expected to decline in many others due to the energy transition. This energy transition is creating the need for bankable investments to convert crude into light olefins. The UOP Integrated Olefin Suite contains the technologies and pathways to provide bankable investments to meet the growing needs for ethylene and propylene with lower cost of production.
Join us to learn more about how Honeywell UOP’s newly launched Integrated Olefin Suite of technologies (IOS) enable novel configurations that convert crude to olefins. Potential benefits include:
- Crude to olefin carbon efficiencies as high as 80% to drive strong, robust operating margins
- Configurations that give 100% net crude to light olefins
- Innovative options to produce niche, higher value by-products such as butadiene and butenes when desired
- Reduced utilities per metric ton of olefin product and options for zero export of fuel by-products
- Potential to significantly increase return on investment over conventional configurations
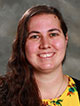
Sponsor: Honeywell UOP
In today’s economy and environment, successful businesses are counting not only every dollar spent, but every molecule emitted. Faced with tightening emission regulations and corporate and/or government commitments to reduce their CO2 footprints, refiners are being faced with mandatory investments not only to comply with the requirements for new units, but to maintain baseline operation in existing plants as well.
Introducing Honeywell UOP’s nViroTM Waste Management Solutions
It’s a new approach to waste effluent treatment, which was designed to help UOP customers in the refining and petrochemical industries meet emission specifications in smarter, more efficient, and more economical ways – to ensure that investments have the biggest impact.
Discover a new way to manage refinery waste treatment. Honeywell UOP presents an educational webinar with Janet Ruettiger, Offering Manager - nViro Solutions, Elizabeth Jensen, Project Development Manager - nViro Solutions and Aric Fisher, Technology Manager - nViro Solutions
Join us and you’ll learn:
- Honeywell UOP’s method to reduce environmental and business risks associated with effluent treatment
- What leading edge technologies are available on the market
- Practical insight from a case study you can use in your own operations
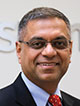
Sponsored by: AspenTech
Hydrogen is playing a key role in meeting the dual challenge of achieving both growth and sustainability initiatives. For over 40 years, AspenTech® has been partnering with industrial leaders to help them meet this dual challenge, by leveraging domain expertise to help organizations run more safely, efficiently and sustainably.
With the need to rapidly expand the deployment of hydrogen production globally, companies must address the challenges of high energy and capex cost of innovation, scale-up and storage to expedite speed to market.
During this webinar, see how AspenTech’s digital solution can enable you to:
- Support and prioritize RD&E alternative innovations for sustainable hydrogen production
- Scale-up new technologies into commercially available pathways
- Minimize cost and risk across the asset lifecycle from technology selection through full scale operations
Register now to join the conversation and hear how you can leverage digital solutions to accelerate progress on your energy transition initiatives.
View On Demand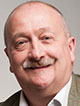
Sponsored by: AVEVA
In the pursuit of a net zero economy, the hydrocarbon processing industries are under enormous pressure to quickly launch and scale up innovative technologies. Carbon capture, bio-based feedstocks, circular chemicals – we need them all now and we need them all big. This webinar will feature a case study of Airbridge’s new CCUS technology that transforms carbon emissions into essential global commodities. Airbridge’s story demonstrates how simulation and digital transformation enable process innovation for sustainable industries. With a high-fidelity process simulation as the foundation, engineers can understand process behavior, scale up quickly and quantify performance. Accurate, accessible data leads to confident investment decisions in a fast-moving market.
View On Demand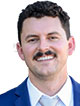
Sponsor: Atlas Copco
The upsurge in interest in hydrogen comes on the back of its exciting potential as a carbon-free energy carrier in mobility and power applications. Historically, hydrogen has been used in refining, chemical processing, steel industries, and ammonia production. Today, the growing momentum for clean fuel and energy has led to enormous opportunities for turbomachinery within the hydrogen supply chain.
Hydrogen liquefaction is one of the few preferred methods to store and transport pure hydrogen. As countries across the world step up efforts to cut greenhouse gas emissions and achieve commitments to net zero by 2050, the demand for hydrogen liquefiers is rising.
Join experts from Atlas Copco Gas and Process and Plug Power as they share insights on LH2 demand, hydrogen liquefaction and reliable turbomachinery design for these demanding processes.
View On Demand
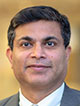
Sponsor: Lummus Technology
As a building block for many useful chemicals, propylene is a flexible, useful and prolific commodity used to make polypropylene, propylene oxide, isopropanol and more. With high demand worldwide, propylene fuels countless end products and chemical processes to meet a wide array of consumer needs.
This webcast will cover:
- Insights from today’s current propylene market, supply and demand
- Technologies that can support increased propylene yields up to 20%
- Processes that can improve efficiency, energy use and provide revamp options.
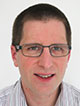
Sponsor: Honeywell
UniSim Design helps engineers create steady-state and dynamic models for plant design, performance monitoring, troubleshooting, business planning, and asset management. UniSim Design enables engineers to complete their work quickly and effectively. This webinar will introduce UniSim Design features and tips and tricks to allow users to get maximum benefit from the time they invest building and working with models.
View On Demand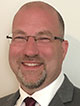
Sponsor: Tracerco
For over 60 years, Tracerco has provided invaluable insights to enable operators to make informed decisions. Its specialist inspection techniques, sophisticated tracers and advanced measurement technologies can accurately and rapidly diagnose a wide range of production issues and problems. Tracerco DiagnosticsTM services can be provided at the hydrocarbon recovery and separation stages of production. These services enable you to optimize the performance of separator systems by measuring online and in real time what is occurring within your offshore assets.
In this webinar, we will discuss how Tracerco’s field-proven technologies can provide immediate real time measurement of any changing process conditions. By identifying issues such as mechanical damage, leaks, deposit build-up, maldistribution, oil in water and liquid carryover, shutdowns can be planned much more efficiently whilst minimizing lost time and associated costs. Register today to learn how we can help you maximize production throughput, reduce operating costs and minimize environmental impact.
View On Demand
- Sumitomo Chemical achieves scale-up of its process for producing propylene directly from ethanol 8/20
- EcoCortec, Jakob Schober GmbH awarded sustainability award for closed-loop circular films solution 8/20
- Sanctions-hit Indian refiner Nayara turns to ‘dark fleet’ 8/20
- EIA: Crude and gasoline inventories fall, distillates rise 8/20
- Czech refinery outage forces Orlen Unipetrol to seek state help to meet diesel demand 8/20
- China’s Sinopec Shanghai Petrochemical first half profit slides 8/20