Webcasts
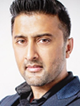
Sponsored by: AspenTech
Frequent shifts in market dynamics and operational constraints make refinery decision-making increasingly complex. Traditional methods for refinery cost analysis and margin modeling struggle to keep pace, leading to inefficiencies and missed opportunities.
Join our industry experts to discover how S&P Global Commodity Insights—in collaboration with AspenTech and AWS—has developed a groundbreaking, cloud-powered refining solution to optimize operations and maximize profitability. Learn how you can use this same solution to:
- Analyze margin impact, maximize throughput and avoid costly shutdowns
- Access refinery insights easily through a cloud-based interface
- Prepare, execute and update program models in real time for faster decision-making
A Q&A session will follow, so please bring your questions. Don’t miss this opportunity to gain valuable insights from industry leaders.
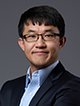
Sponsored by: AspenTech
Mandated to aggressively reduce emissions, today’s refining and chemical companies must also find new ways to improve energy efficiency and—in turn—margins. The sooner owner/operators uncover opportunities for improvement, the faster they can advance operational excellence goals.
Join experts from AspenTech® and Samsung E&A as they share innovative digital tools and services that help companies quickly identify cost-saving, emission-reducing measures. Learn how this new partnership enables you to:
- Explore low-CAPEX energy projects around areas such as heat integration
- Make incremental or larger gains in energy efficiency—and profitability
- Take a strategic approach in accelerating energy optimization across assets
You’ll hear case studies of how companies are using these same tools and methodologies to achieve significant, measurable results. If you’re responsible for energy efficiency, emissions reduction and technical services within your organization, you won’t want to miss this webinar.
View On Demand
Sponsored by: Lummus Technology
The pervasiveness of per- and polyfluoroalkyl substances (PFAS) in the environment and how to deal with their contaminating effects, treatment and destruction has been an active societal discussion in recent years, especially given how it affects one of our most valuable resources—water.
PFAS contamination shows up in our drinking water, municipal and industrial wastewater, remedial activities, landfill leachates, sludge disposal, agriculture and more. End users, regulators and technology suppliers are racing to solve this problem, developing solutions for PFAS collection and removal, as well as treatment, specifically in offsite disposal and destruction, as well as localized, onsite destruction.
This webcast will cover:
- A comparison of advantages and disadvantages of destroying PFAS waste offsite versus onsite
- An economic comparison of the associated PFAS waste disposal techniques
- Lummus’ Zimpro Electro Oxidation technology and its ability to handle long- and short-chain PFAS with an overall mass balance of fluoride in the process
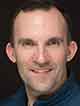
Sponsored by: dataPARC
In the Manufacturing 4.0 era, downstream oil & gas producers have more data at their fingertips than ever, offering the promise of higher production rates, more consistent quality, and reduced costs through data-driven strategies.
Standing between many businesses and this promise of process optimization are questions surrounding the right tools to harness this data effectively.
Join us as we discuss:
- A framework for understanding and categorizing the current industrial analytics landscape
- The roles new AI and machine learning applications play in optimizing processes
- Methods for migrating from legacy systems
- A firsthand look at the solutions dataPARC can offer in this evolving space

Sponsored by: AspenTech
Frequent changes in refinery operating conditions cause planning models to fall out of sync with actual conditions, making them less reliable. At the same time, updating these models is complex, often forcing refineries to turn to expensive third-party consultants.
Join our experts to discover how the latest innovations in Industrial AI and Aspen HYSYS® process simulation can help you:
- Reduce the time and effort needed to update planning models
- Maintain model accuracy for a longer period of time
- Update models in-house, without having to rely on costly third-party consultants
A Q&A session will follow so please come prepared with your questions.
View On Demand
Sponsored by: Lummus Technology
Global hydrogen demand is forecast to significantly increase over the next few decades, with hydrogen produced with low and zero carbon intensity emerging as a transformative solution to decarbonize industries critical for modern life. Lummus’s advanced hydrogen and carbon capture technologies stand to help industrial operators to meet emission regulation requirements and economically achieve low and zero carbon intensity production.
This webcast will introduce several of Lummus’ hydrogen technologies, including:
- SMR, ATR grey and blue, and green hydrogen technologies
- Advanced reactors
- Carbon capture technologies
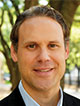
Various trends, regulations and initiatives are affecting global and regional spending in the hydrocarbon processing sector. These factors are leading to new grassroots installations, expansions, and conversions, and, conversely, consolidation and rationalization.
Join Lee Nichols, Vice President, Content/Editor-in-Chief, Hydrocarbon Processing, as he navigates the future of capital spending in the refining, petrochemicals and gas processing/LNG industries. This webcast will provide the major economic, environmental, regulatory and industry trends impacting capital spending for the year ahead.
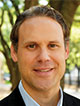
Join us for an exclusive webcast, during which Gulf Energy Information's expert editors will deliver deep insights into President Trump’s policies' impact on global energy markets. This webcast will explore recent shifts in U.S. energy policies and their global repercussions. Key topics include regulatory changes, adjustments in subsidies and taxes, and potential impacts on the oil, gas, and renewable energy sectors worldwide.
We will explore the ramifications of the U.S. emerging as a net energy exporter and its impact on global supply chains, as well as evolving trade relations and geopolitical alliances with major oil players like OPEC, Russia, and China. The webcast will also examine energy security, geopolitical risks, and emerging trends in renewable energy investments.
Additional discussions will focus on technological innovation, energy transition, and the role of AI in adapting to policy changes. Finally, we’ll explore how these developments may influence future energy prices, demand, and the overall market landscape.
View On Demand
- Britain will not bail out bioethanol industry hit by Trump trade deal 8/15
- Russian energy facilities targeted recently in drone attacks 8/15
- Shell: Norco, Louisiana (U.S.) refinery gasoline unit work to start on Friday 8/15
- Sanctions-hit Indian refiner Nayara in talks with govt to sustain operations 8/15
- The API challenges Trump plan to cut biofuel import credits 8/15
- IAG selects record 29 startups for accelerator program 8/15