Webcasts
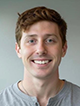
Sponsored by: AspenTech
Explore a new dynamic modeling approach that offers flexible online optimization and caters to a wide range of applications, including broad production envelopes, high-value reactors and small-scale column applications. With the new enhancements in Aspen GDOT™ V15, refineries and olefins plants can select the optimal scope for their needs, achieving optimum molecule recovery, improving energy utilization and accelerating value delivery with minimum resource expenditure.
Learn how to achieve quicker and simpler energy optimization using Aspen Unified GDOT Builder, which now enables:
- Small scope distillation applications that maximize product recovery and energy efficiency with existent and new column templates blocks
- Enhanced process reaction modeling with improved control over reactor conversion, recovery and recycles with less customization
- Faster energy integration optimization in crude distillation units with heat integration templates
Don't miss this opportunity to learn how you can transform your approach to molecule recovery and energy integration. Register now to secure your spot and stay ahead in the dynamic world of process optimization.
View On Demand
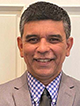
Sponsored by: Chevron Lummus Global
With today’s economic challenges impacting our industry, it is imperative that refiners evaluate their existing assets and look for innovative, low-capital solutions to identify gross margin improvement opportunities. There are several significant revamp methodologies that fit refinery operators who are considering capacity expansions, product quality improvements and flexibility enhancements for their facilities.
In this webcast, Chevron Lummus Global will examine several use-cases that highlight substantial gross margin value capture via hydroprocessing units using catalyst volumes that are repurposed to produce higher margin products in both conventional fossil fuel and renewable fuel applications.
The case studies will include:
- Converting a hydrocracking unit to renewable fuel application for SAF production
- Increasing the fresh-feed capacity of a two-stage recycle full conversion hydrocracker by modifying the second stage to process a combination of fresh feed and first-stage unconverted oil
- Converting a residuum desulfurization unit (RDS) into an integrated RDS and hydrocracking system
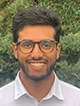
Sponsored by: AspenTech
As operational demands increase and margins tighten, it’s no longer enough to rely on traditional predictive maintenance practices. To stay competitive, companies must embrace a more integrated, proactive approach to Asset Performance Management (APM)—one that combines AI/ML, safety-first maintenance practices, and smarter investment planning to transform asset management.
Join Kiran Darmasseelane, Principal Analyst at Verdantix, and experts from Emerson and AspenTech® for a dynamic panel discussion exploring the evolution of APM beyond predictive maintenance. Discover how to:
- Reduce risk and improve reliability with embedded FMEA-driven decision workflows
- Improve safety and environmental compliance within maintenance strategies
- Accelerate AI agent training to resolve issues faster and with greater confidence
- Align OPEX and CAPEX planning with long-term asset strategy for greater value
Don’t miss this opportunity to gain expert insight and hear how industry leaders are unlocking greater long-term value from their assets.
View On Demand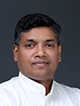
Sponsored by: Honeywell UOP
The sustainable aviation fuel (SAF) market is growing rapidly due to the need to reduce greenhouse gas emissions and shift to sustainable energy sources. Honeywell offers tailored solutions for producing (e)SAF from non-fossil waste like biomass, municipal solid waste (MSW), biogas, CO2, and H2 using Honeywell’s FT UnicrackingTM technology. Honeywell’s FT Unicracking technology can enable production of low carbon, carbon neutral, and even carbon negative (e)SAF depending on the feedstock used and plant configuration which supports compliance with government mandates like the ReFuelEU Aviation initiative and potential qualification for incentives like 45z under the US Inflation Reduction Act (IRA).
Join our webinar to learn how Honeywell FT Unicracking Technology portfolio helps bringing technology and execution advantage to make (e)SAF production more cost-effective, bankable and easy to implement for project developers and advanced refiners investing in the energy transition by producing (e)SAF or renewable diesel.
View On Demand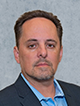
Sponsored by: Lummus Technology
As industries continue to push for net zero emissions, companies and decision-makers seek to employ economically feasible processes and technologies to meet regulations and targets. But what if you could kill two birds with one stone?
Hydrogen rich fuel can be obtained from a simplified steam methane reformer (SMR) using sulfur-free methane obtained from the ethylene plant. In this novel scheme, feed pretreatment is not required. After passing through the SMR, a low-pressure shift reactor converts CO to CO2. Water is removed by condensation and CO2 is removed by an appropriate technology. This almost CO2-free stream rich in hydrogen is used as a fuel instead of conventional methane fuel. For many plants, there is no need to change the burners in the cracking heater.
This webcast will cover:
- The integration of hydrogen with the ethylene heater and its impact on CO2 reduction
- How to reduce CO2 emissions by more than 60% without reducing SHP steam production levels
- Insights and plans for implementing in existing and new heater designs
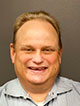
Sponsored by: Emerson
In a world shaped by globalization, rapid technological evolution, shifting consumer expectations, and stringent regulatory demands, automation is no longer optional—it’s essential. This webinar dives deep into how modern automation technologies are redefining operational strategies, helping businesses reduce costs, enhance productivity, and stay ahead of the competition.
Join us on April 29, 2025, in partnership with Hydrocarbon Processing, for an interactive exploration of how automation can become a cornerstone of operational excellence. Discover actionable insights into:
- Reducing operating costs while maximizing facility performance and utilization.
- Enhancing equipment reliability and availability while cutting maintenance expenses.
- Strengthening workplace safety through advanced automation solutions.
- Realizing ROI from sustainability initiatives while driving long-term value.
Through a holistic approach spanning production, reliability, safety, and sustainability, this webinar provides the strategies and tools needed to unlock your organization's full potential. Gain practical answers, real-world examples, and a roadmap to leverage automation as a catalyst for lasting success.
View On Demand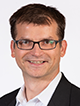
Sponsored by: Honeywell
As refiners and petrochemical producers move towards a more decarbonized value chain, while balancing the needs of remaining competitive and ensuring workforce competency, operators must develop new digital muscle by using an Intelligent Operations Framework through:
- Harnessing ubiquitous sensors, digital twin, and virtual technologies
- Embedding process knowledge into automation
- Humanizing artificial intelligence for future-ready operations
With decades of experience in process control and automation and being in lockstep with leading process technology licensors, Honeywell technology delivers industry leading returns to our partners by:
- Embedding proprietary knowledge in automation systems – de-risking and accelerating project schedules
- Leveraging cyber secure edge, cloud and virtual technologies – delivering safe, scalable and leaner designs
- Using analytics, AI and ML technologies – enabling a sustainable and future ready operations
Join Honeywell on how you can decarbonize with Honeywell’s Intelligent Operations Framework, fusing sensors, digital twins, and AI-driven automation to continue your journey towards a sustainable, future-ready digital refinery or petrochemical plant.
View On Demand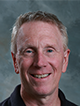
Sponsored by: Honeywell UOP
In the hydrocarbon processing industry, waste heat is often an untapped resource—yet it holds the key to reducing costs, improving efficiency, and staying ahead of the competition. This webinar introduces our cutting-edge chemical heat transformer technology, which converts waste heat into valuable industrial heat with exceptional efficiency.
But technology alone isn’t enough. A game-changer in this space is the strategic alliance between Honeywell UOP & Qpinch, designed to streamline implementation and maximize benefits for your operations. We’ll explain what this alliance means, how it simplifies adoption, and why it sets a new standard for efficiency projects.
We’ll also showcase real-world use cases and explore flexible business models, including CAPEX investments and service-based options. Don’t miss this opportunity to rethink waste heat utilization, gain a competitive edge, and leverage strategic partnerships for long-term success.
View On Demand
- Britain will not bail out bioethanol industry hit by Trump trade deal 8/15
- Russian energy facilities targeted recently in drone attacks 8/15
- Shell: Norco, Louisiana (U.S.) refinery gasoline unit work to start on Friday 8/15
- Sanctions-hit Indian refiner Nayara in talks with govt to sustain operations 8/15
- The API challenges Trump plan to cut biofuel import credits 8/15
- IAG selects record 29 startups for accelerator program 8/15