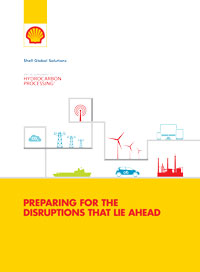
Preparing for the disruptions that lie ahead
Preparing for the disruptions that lie ahead
Over the last four decades, refiners have had to adjust to a relentless stream of changes in product demand patterns and ever-more-stringent environmental regulations. Making the adjustment takes time and requires a good assessment of the potential future scenarios.
Key steps for refiners ahead of IMO 2020
The reality is that many refiners remain unprepared for the International Maritime Organization’s (IMO) MARPOL 73/78 Annex VI (IMO 2020). These regulations, which will substantially tighten the global cap on the maximum sulphur content of marine fuel oil, could have a major impact on an ill-equipped refiner’s profitability. Fortunately, it is not too late; they could implement several low-cost solutions over the next two years to safeguard their competitive position.
The evolving mobility mix – potential impacts on refiners
From climate change, air quality concerns and the growth in electric vehicles through to the emergence of smart cities and autonomous vehicles, a complex mix of interrelated factors is changing conventional patterns of energy supply and demand – and at a faster rate than most industry managers recognise. What are the implications for refiners and how could they respond?
Seeing the integrated picture
Finding ways to minimise the amount of bottoms sent to the bunker fuel pool has become a strategic priority for many refiners. Although many technical solutions are available, the optimum response for a specific refiner depends on individual circumstances. Refiners that already have a visbreaker unit (VBU) and are capital constrained may find integrating it with the vacuum distillation unit (VDU), solvent deasphalting (SDA) unit and hydrocracking unit (HCU) or fluidised catalytic cracker (FCC) to be particularly attractive. Here is why.
How innovations in FCC feed nozzle technology can help in responding to the bunker fuels challenge
Few refiners will respond to the International Maritime Organization’s global fuel oil sulphur cap (IMO 2020) with a single, major investment that will eliminate the bottom of the barrel. Most will implement several low-capital-expenditure solutions that partially reduce it. One relatively inexpensive option that may be particularly attractive is an innovation in fluidised catalytic cracking (FCC) feed nozzle technology, previously thought to be a mature technology. Recent developments here provide the opportunity to increase slurry oil conversion through better atomisation and to, therefore, reduce this heavy, high-sulphur stream, which traditionally goes to the marine fuel oil pool.
Turning IMO 2020 to your advantage with the Scot<sup>1</sup> Ultra Process
Time to prepare for the new marine fuel sulphur specifications is rapidly running out for refiners. Many residue conversion options are available, including quick-win solutions. For example, the Shell Claus off-gas treating (SCOT) ULTRA process offers the potential to increase sulphur recovery unit (SRU) capacity by up to 30% quickly and without capital expenditure, while cutting tail gas treating unit operating costs by up to 50%.

- Aster Chemicals declares force majeure at Singapore naphtha cracker 8/29
- Orlen signs 1-yr deal with Equinor for supply of 15% oil it uses 8/29
- Novatek partially resumed processing at Ust-Luga complex 8/29
- Phillips 66 to begin winding down Los Angeles-area refinery next week 8/29
- Update: Mexico's Minatitlan refinery back online, Olmeca still down 8/29
- SIBUR produces test batch of first hexane plant in Russia 8/28